After years of testing various prototypes, Kevin eventually landed on a solution which, in his words, would provide people with a “seamless experience for serving wine”.
Cooler than cool and set to become one of the drinks industry’s biggest disruptors, Kaelo uses a patented dry-cooling system, previously only used by innovators in the medical sector and the military, to maintain the temperature of a bottle of wine once opened to within 1-2 degrees of its original temperature.
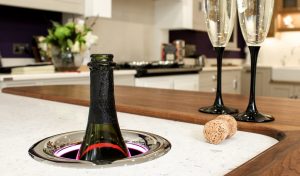
“We officially launched Kaelo onto the market in 2016 but I’ve been working on the design and technological aspects for the best part of a decade.” Kevin said. “Having enjoyed great success so far across the residential, commercial and marine markets, the business has grown organically over time and we now have customers across the globe, but I had a vision to make the product more accessible, so that eventually the Kaelo would become a must-have item in every modern kitchen”
Hand-built in a range of luxury finishes, the cylindrical design of Kaelo combined with the high levels of tech meant that engineering the parts was both tricky and expensive.
Kevin and the team set about finding a solution which would streamline Kaelo’s manufacturing process to minimise costs and make the product more affordable, without compromising the product’s seamless design. After looking into a variety of different material options and speaking to a number of different companies, Kevin came across North East-based, Omega Plastics Group.
Specialising in custom tooling and plastic injection moulding, the award-winning Omega Plastics Group provides a full turnkey solution for companies operating across the FMCG, automotive, healthcare, aerospace and industrial/technical product sectors to help bring its customers’ products and innovations to life.
“Omega Plastics Group immediately stood out from the crowd,” Kevin commented.
“Being new to the world of plastics, we needed to work with a company who knew the process inside out, who could guide Kaelo through it from start to finish. Omega Plastics Group has worked with businesses of all shapes and sizes and the team’s knowledge of the moulding and tooling aspects of the process is fantastic.
“Having everything housed under one roof made getting refinements to the design really straightforward. Our project manager, Iain, handled everything and explained the process to us in plain English which was really encouraging. We knew we weren’t going to get it right first time, but the team seem to thrive off accepting new challenges and were really supportive.”
“Both teams at Omega Plastics and Kaelo worked closely throughout the manufacturing process to identify improvements and refinements that made the product more accessible to mass markets without compromising on the quality and design. Kevin, Dario and their team were always available to talk through our findings and even suggested additional options themselves which allowed us to move through the project at pace. All this made for a great working relationship with mutual respect which inevitably enabled us to deliver the products to a high quality, on time and in budget.”
Iain Lyon, Project Manager at Omega Plastics.
Find out more about our work with FMCG clients.
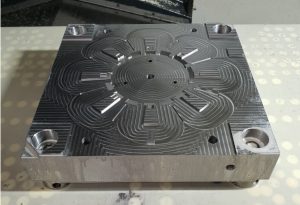
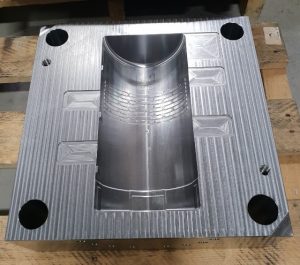